A company specialized in fabricating insulation boards, reached out to us with several challenges they encounter during their production process.
Producing insulation materials requires precise handling and an efficiently operating belt, so aligning the material on the belt properly is critical.
Prior to contacting us, the company relied on an air atomizing system to spray the release agent. However, the lack of monitoring on the production belt caused unexpected stops and production delays. Additionally, the air atomizing nozzles created a mist of compressed air, resulting in excessive fog in the production area.
Solution
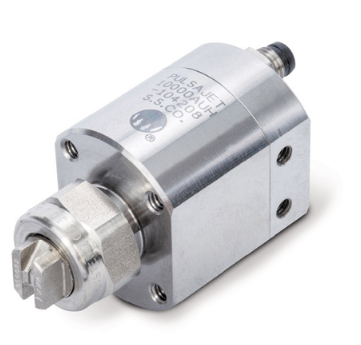
Choosing Spraying Systems Co.® means partnering with a spray technology leader with over 85 years of expertise.
The application of a coating release agent demands precise and efficient spraying to reduce waste. To validate our solution, excessive lab testing was conducted using the release agent that was diluted in water.
Ultimately, our spray experts decided our PulsaJet® nozzles were the perfect choice in this situation. The stainless-steel tip of our nozzle ensures accurate and precise delivery, minimizing waste and reducing chemical fluid costs.
With a closed-loop system control, provided by the AutoJet® E2850+ spray controller, the flow rate automatically adjusts to maintain the correct volume of release agent. This state-of-the-art system enables independent control of the spray volume for two nozzles across two separate zones. This top-notch nozzle also features a high turn down ratio, allowing a wide range of flow rates without any change in spray performance.
To ensure reliability, the system includes a flow meter to monitor for nozzle clogging and a liquid selection valve for easy cleaning. Together, this setup delivers precision, efficiency, and cost savings for optimal coating release agent application.
Result
Our customer was highly impressed with the performance of our PulsaJet® nozzles. On top of that, they are using up to nine times less chemicals each year since the system was installed, which results in an ROI of three months.
The project's ultimate goal was achieved: implementing a reliable system which reduces the releasing agent costs and eliminates unexpected breakdowns.
These improvements not only deliver significant cost savings for our customer, but also promote a more sustainable and efficient production process.