L'une des principales entreprises de l'industrie du caoutchouc recherchait un système de revêtement par pulvérisation de silicone et de polymère pouvant être appliqué juste avant l'emballage de ses produits (tels que les joints de fenêtre en caoutchouc).
Auparavant, elle utilisait des buses standard, contenues dans des cabines de pulvérisation, pour pulvériser le caoutchouc de haut en bas. Ces cabines étaient équipées d'une installation d'extraction pour éviter la formation d'un brouillard excessif. Pour les revêtements plus fins, ils utilisaient des buses de pulvérisation à air et pour les revêtements plus épais, des bains d'immersion.
Aucune de ces méthodes ne donnait le résultat escompté et leur réparation était coûteuse et inefficace. L'excès de liquide était à l'origine de la plupart des problèmes et entraînait en fin de compte des problèmes de qualité et des clients mécontents.
Pour mettre fin au gaspillage lié à la sur-application de liquides - puis à l'application de solutions coûteuses pour se débarrasser de l'excès de liquide - le producteur de caoutchouc a décidé de chercher une nouvelle solution. Celle-ci devait être plus durable, limiter les coûts et éviter un espace de travail pollué, source de conditions dangereuses pour les travailleurs.
Système de revêtement par pulvérisation de silicone et de polymères AutoJet

En tant que partie intégrante de la principale entreprise mondiale de technologie de pulvérisation, notre ingénieur local Spraying Systems a été contacté pour partager son avis d'expert sur la question. Après une évaluation minutieuse, il a proposé l'installation d'un système AutoJet® 2008+ à deux canaux - pour utiliser séparément les revêtements de silicone et de polymères. Le système était équipé de buses PulsaJet® pour réduire considérablement le volume de liquide pulvérisé.
Après une première démonstration sur site, le client a accepté de faire un test sur une période prolongée, ce qui est essentiel pour un processus aussi vital. De cette façon, il pouvait évaluer le potentiel de réduction des coûts de la solution et garantir la qualité et la satisfaction du client.
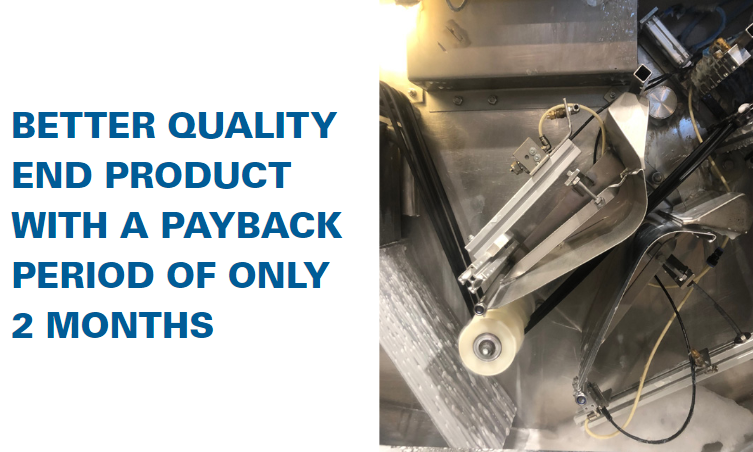
Résultat
Après la phase de test, notre client a été heureux de constater que le système fonctionnait comme prévu. La décision a été prise immédiatement de déployer la solution sur l'ensemble de ses 8 lignes de production.
Les améliorations en matière de durabilité ne sont rien moins qu'impressionnantes. Ce changement relativement mineur a permis de réduire considérablement la consommation d'énergie, l'utilisation de produits chimiques et les émissions. L'environnement de travail plus propre a également permis d'améliorer considérablement la sécurité sur le lieu de production.
Outre les améliorations en matière de durabilité, le producteur de caoutchouc bénéficie également d'un meilleur processus de production. Les temps d'arrêt sont considérablement réduits et l'amélioration de la qualité du produit signifie que les clients finaux sont également satisfaits.
Les économies réalisées sont si importantes que le client a rentabilisé la solution proposée en deux mois seulement.