Jedna z wiodących firm w branży gumowej poszukiwała systemu do natryskiwania powłok silikonowych i polimerowych, który mógłby być stosowany tuż przed pakowaniem jej produktów (takich jak gumowe uszczelki okienne).
W przeszłości używali oni standardowych dysz umieszczonych w kabinach natryskowych do natryskiwania gumy od góry do dołu. Kabiny te były wyposażone w instalację odciągową, aby zapobiec nadmiernemu zamgleniu. W przypadku cieńszych powłok stosowano dysze rozpylające powietrze, a w przypadku grubszych powłok kąpiele zanurzeniowe.
Żadna z tych metod nie dawała wymaganego rezultatu, a ich naprawa była kosztowna i nieefektywna. Nadmiar cieczy powodował większość problemów i ostatecznie prowadził do problemów z jakością i niezadowolonych klientów.
Aby przezwyciężyć nieekonomiczny proces nadmiernego nakładania płynów - a następnie stosowania kosztownych rozwiązań w celu pozbycia się nadmiaru płynu - producent gumy postanowił poszukać nowego rozwiązania. Musiało ono być bardziej zrównoważone, ograniczać koszty i zapobiegać zanieczyszczeniu miejsca pracy - powodując tym samym niebezpieczne warunki dla pracowników.
System AutoJet do natryskiwania powłok silikonowych i polimerowych

Jako integralna część wiodącej globalnej firmy zajmującej się technologią natryskiwania skontaktowaliśmy się z naszym lokalnym inżynierem ds. systemów natryskiwania, aby podzielił się swoją ekspercką radą w tej sprawie. Po dokładnej ocenie zaproponował on instalację systemu AutoJet® 2008+ z dwoma kanałami - do stosowania oddzielnie powłok silikonowych i polimerowych. System został wyposażony w dysze PulsaJet®, które znacznie zmniejszają objętość rozpylanej cieczy.
Po wstępnej demonstracji na miejscu, klient zgodził się na przeprowadzenie testu w dłuższym okresie czasu - co jest niezbędne dla tak ważnego procesu. W ten sposób można było ocenić potencjał oszczędnościowy rozwiązania oraz zapewnić jakość i zadowolenie klienta.
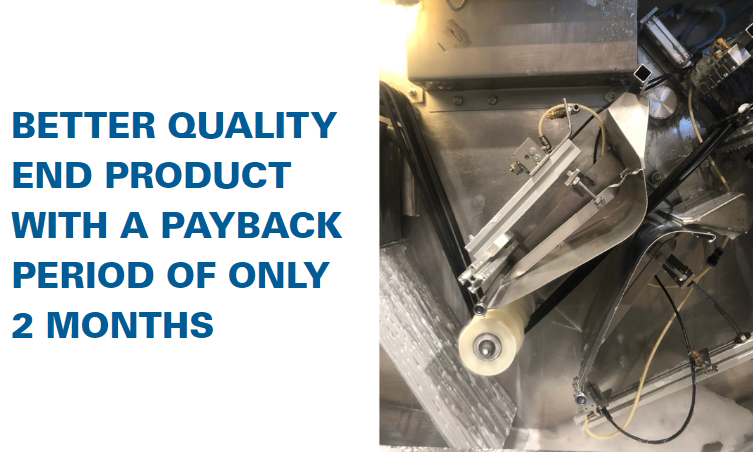
Rezultat
Po zakończeniu fazy testowej nasz klient z zadowoleniem stwierdził, że system działał zgodnie z oczekiwaniami. Natychmiast podjęto decyzję o wdrożeniu rozwiązania na wszystkich swoich 8 liniach produkcyjnych.
Poprawa w zakresie zrównoważonego rozwoju jest wręcz imponująca. Już po wprowadzeniu tej stosunkowo niewielkiej zmiany nastąpiła ogromna redukcja zużycia energii, substancji chemicznych i emisji. Czystsze środowisko pracy znacznie poprawiło również bezpieczeństwo na hali produkcyjnej.
Oprócz poprawy zrównoważonego rozwoju, producent gumy doświadcza również poprawy procesu produkcyjnego. Przestoje zostały znacznie zredukowane, a lepsza jakość produktu oznacza, że klienci końcowi są również zadowoleni.
Łączne oszczędności są tak ogromne, że klient osiągnął całkowity zwrot kosztów proponowanego przez nas rozwiązania w ciągu zaledwie 2 miesięcy.